Understanding Chip Antennas
Antenna Chip Overview - Using This Designer Guide
Johanson Technology, a global leader in chip antenna design, manufacturing, implementation, and technical support, has prepared this technical handbook, with the aim of educating and informing customers and newcomers about chip antennas. This booklet includes the types of ceramic chip antennas and their applications that Johanson offers, advantages of Johanson's antennas over other types, considerations when choosing chip antennas and how to properly install and tune each antenna for impressive high-frequency ceramic solutions.
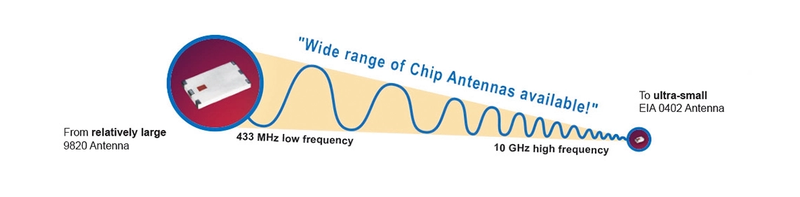
Johanson Technology offers a wide range of chip antenna products that operate in various bands from 433 MHz to 10 GHz. These antenna chips are available in numerous sizes, from ultra-small EIA 0402 to relatively large EIA 9820. Each optimized for its intended application where PCB antenna placement location, size, performance, and cost are considered.
Typical uses for Johanson chip antennas include nearly all small battery-operated wireless applications including: IoT, Bluetooth, WiFi, UWB, GPS/Glonass, LoRa, NB-IoT as well as other ISM band applications. Other uses include wearable healthcare monitoring devices, portable devices, weight constrained devices, low profile devices and many more applications where the antenna must be mounted on a PCB.
Most chip antennas are designed to have omnidirectional radiation patterns and peak gain near 0dBi. Average gain may be a few dBi lower. To achieve this omni-directional radiation pattern, the antenna requires a specific ground. When the antenna is a monopole structure, it uses the top layer of the PCB ground as the other monopole to complete the dipole. This is why the PCB top RF ground plane is so critical.
While Johanson's chip antennas may appear similar externally, their internal structures vary significantly. As a result, certain critical parameters must be taken into account to achieve optimal performance.
The circuit designer must recognize that all of the following seven factors influence the antenna's final performance. . .
- The Chip Antenna, with its associated internal circuitry.
- The PCB "No-Ground" or “Metal Keep-Out” area & the geometry defined on the data sheet.
- The Chip Antenna placement relative to the edge of the circuit board.
- The specified Vias.
- Conductive components placed very close to the "No-Ground" area (especially if tall in Z axis).
- The matching network. If possible, a matching Pi-network is recommended although some Antennas will work with a T-network. Accurate values can only be determined with benchtop tuning.
- The Enclosure
It is vital to note that making improper alterations to the no-ground area or chip locations relative to the edge of the circuit board may lead to substandard performance.
Also, violating any of the previously mentioned points can cause a degradation in antenna performance.
Johanson antennas are constructed using a variety of techniques, including monopole, dipole, folded loop, inverted-F, and inverted-L designs.
In addition, when it is not possible to have the required no-ground area for an antenna, we've developed a solution. A chip antenna that can be placed directly over a ground plane. This design is unique in the industry.
Technology Discussion (LTCC)
Johanson Technology chip antennas are produced using Low Temperature Co-Fired Ceramic (LTCC) technology. LTCC technology is a type of multi-layer ceramic process that allows for the integration of very small passive components such as capacitors and inductors into a single package. LTCC technology enables the production of miniaturized and highly functional electronic components, modules, or systems with improved performance, reliability, and cost-effectiveness
antenna.
This LTCC technology involves the fabrication of a multi-layer ceramic substrate by screen-printing ceramic green tapes with conductive, resistive, or dielectric inks. The LTCC process enables the integration of multiple layers of circuitry, similar to a multi-layer PCB, which can be interconnected through vias, to form complex three-dimensional structures.
The advantages of LTCC technology include a consistent dielectric constant around the antenna elements near field, size, capacitive coupling resiliency, SMT for high-speed volume manufacturing, high reliability and stability at high temperatures, excellent electrical properties, low signal loss, and high dimensional accuracy. LTCC technology is widely used in various applications, including RF and microwave communication systems, automotive electronics, medical devices, and industrial automation. These chip antennas are designed to be compact and can be integrated into a wide range of electronic devices such as IoT sensors, mobile phones, laptops, Bluetooth headsets, and other small, typically portable, wireless devices.
Some of the key features of LTCC technology include but are not limited to:
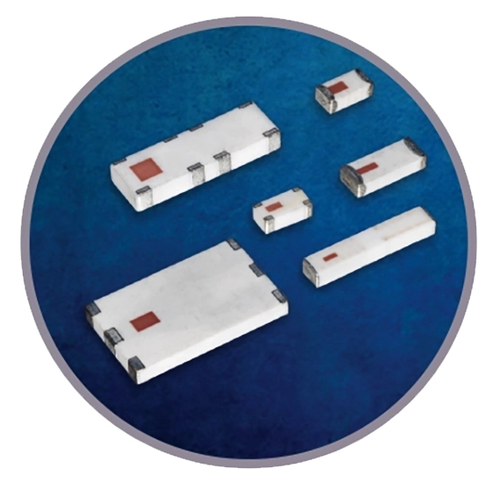
- Miniaturization: LTCC technology enables the mass production/fabrication of compact and highly functional electronic components and modules.
- High-frequency operation: LTCC technology provides excellent electrical properties for RF and microwave applications.
- Highly repeatable & consistent process for volume applications that provides high yields of RF circuits and components.
- Thermal stability: LTCC technology offers high thermal conductivity, low thermal expansion, and high resistance to thermal shocks, making it suitable for high-temperature and temperature swinging applications.
- Integration: LTCC technology allows the integration of multiple components and circuits into a single package, reducing the need for external components and improving system performance.
- Customization: LTCC technology offers flexibility in design and manufacturing, enabling customization for specific applications and requirements.
- Reduction of time-to-market: Due to the aforementioned, LTCC reduces the number of prototype spins and iteration, effectively reducing the product’s development lead-time.
When To Use Antenna Chips & PCB "No Ground" Areas
When to use Antenna Chips:
Antenna Chips are highly effective and commercially attractive when system requirements include one or more of the following:
- Small compact packages
- Large volumes
- The operational frequency band is above 433MHz
- 4 watts (CW – Continuous Wave) or less of transmit power at the antenna.
- The antenna can be located directly on the circuit board.
- Omni directional radiation pattern performance is preferred.
When not to use Antenna Chips
Antennas Chips are often not the best solution when system requirements include one or more of the following:
- Higher than 4 watts (CW – Continuous Wave) output power at the antenna is required.
- The antenna needs to be physically located away from the circuit board.
- Replacing whip antenna while still requiring the same gain.
- The system requires directional antenna performance or an effective antenna average gain of 3dBi or more
"No-Ground" or "Keep-Out" Areas Antenna (Chip) Overview
A ground plane is typically used with an antenna chip to provide a reference plane for the antenna and to improve its performance. For Johanson antennas, a ground plane must be included.
The ground plane is an integral part of the overall antenna system design. The size of the ground plane can vary. For example, if a customer only needs one cm of range, then the ground plane can be minimal. If the customer requires 30m, then the ground size and fluidness are critical.
When Johanson designs antenna ceramic chips, there are some basic requirements established prior to conception. Some of these requirements include the size of the PCB and clearance area, gain, radiation pattern, efficiency and the type/amount of ground required.
During the optimization process which typically includes creating a uniform radiation in the desired axis, the designers at Johanson use a "no-ground" area and its geometry on the PCB as one of the key features to optimize radiation pattern performance. This "no-ground" area is critical to the final antenna performance.
It is important to note that the "no-ground" or “keep-out” area must extend down through all layers of a multilayer PCB.
However, it's important to note that while Johanson antenna chips may function with changes to the "no-ground" area, their performance may be less predictable and less efficient compared to the same antenna chips with a specified "no-ground" area. Therefore, it's important to carefully consider the requirements of your specific application and consult with the Johanson's technical team when considering changes to the "no-ground" area.
Unique Solution - Chip Antenna Over Ground Plane!
"No-Ground" or "Keep-Out" Areas Antenna (Chip) Overview
The only chip antenna over ground plane! The chip antenna mounts directly above or below the metal layer of PCB (Printed Circuit Board). No antenna clearance required ever again!
Johanson Technology has developed this unique chip antenna solution that eliminates the need for “No-Ground” area around the antenna. In this solution, the antenna is designed to have a solid ground plane directly underneath the antenna. This is a novel solution and used when the system configuration does not allow for the necessary “No-Ground” area or regional clearance of metal required by most chip antennas.
Common Applications:
- Wearable devices
- Portable Audio
- Sensors
- Tag, Tracers, iBeacon
- Home Automation/RF Locks
- Advanced Thermostats
- POS/Payment Systems
- In-Vehicle WiFi
- WiFi Access Points
- Chipset Specific FEMs
- Portable Positioning Modules
- Vehicle/Insurance Tracking
The Manufacturing Process
The LTCC manufacturing process typically involves the following steps:
The LTCC process starts with the preparation of the ceramic powder and other materials. The ceramic powder is mixed with organic binders and solvents to form a homogeneous slurry, which is then processed into ceramic green tapes of the desired thickness and dimensions.
Screen printing: The green tapes are then screen printed with conductive, resistive, or dielectric inks to form the desired circuit pattern. The ink is deposited onto the green tape using a fine mesh screen, which is pressed against the tape and moved along its surface. The ink is then dried to remove the solvent and binder.
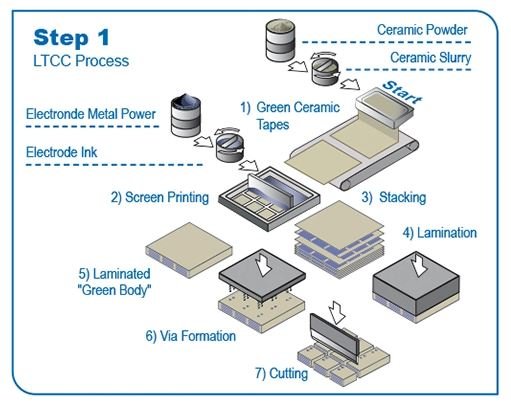
Lamination: Multiple layers of green tapes with different circuit patterns are then stacked on top of each other and laminated together using a combination of heat and pressure. The resulting laminated structure is called a "green body".
Via Formation: Vias are then created in the green body to interconnect the different layers of circuitry. This is typically done by drilling or punching small holes through the green body and filling them with conductive paste.
Cutting: The substrate is then cut, singulation of the individual components.
Firing: The green body is then fired in a furnace at a low temperature (typically between 850°C and 1000°C) to remove the organic binders and sinter the ceramic particles, resulting in a dense and co-fired ceramic substrate. The conductive, resistive, and dielectric inks are also fired, creating the desired electrical properties.
Termination: The fired ceramic components are inspected for defects and then the termination paste is applied in the form of dipped termination or printed land pattern terminations. These terminations, also called solder pads, perform the electrical connections to the circuit board.
Finally, at Johanson, antenna chips undergo rigorous RF testing to ensure that only fully functional parts are delivered to our valued customers.
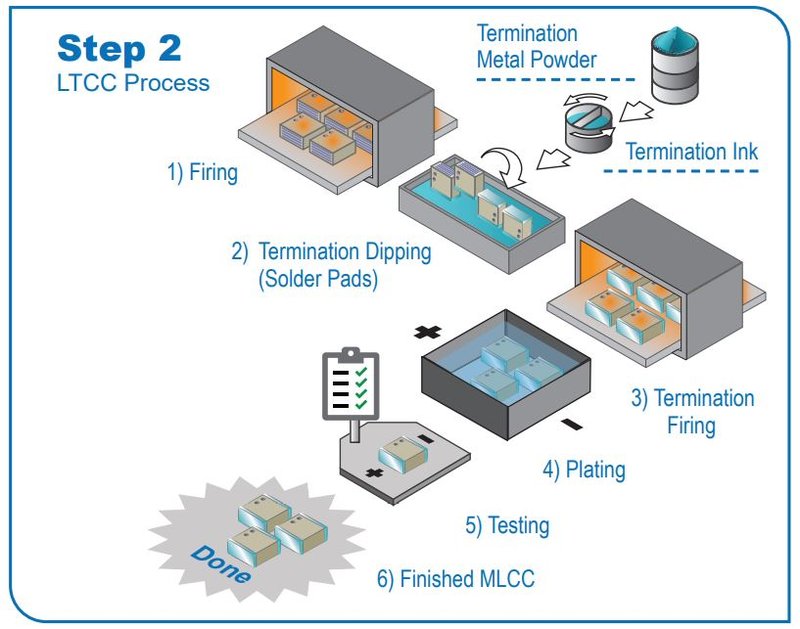
The LTCC process can be modified and customized to suit specific applications and requirements. For example, different materials with various dielectric properties can be used for the ceramic powder, and the firing temperature can be adjusted to achieve specific electrical and thermal properties. These different powders provide various k and loss tangent values allowing our component designers to achieve unique solutions.
Current Offering and Why Not Lower Then 433MHz
Frequency Range (Overview)
The frequency range is described as the upper and lower frequencies where acceptable radiation pattern, gain, and return loss performance is achieved. Typically, Johanson Technology antennas are optimized with the associated ground-plane to exhibit the desired radiation pattern performance and a typical 9.5dB return-loss over the band in question
Current Offering (Frequency Range Overview)
The frequency range of chip antennas can vary depending on their design and construction. Generally, Johanson chip antennas are designed to operate in narrow frequency ranges from 433 MHz to 10 GHz.
Most Johanson Technology chip antennas operate in ultra-high-frequency (UHF) chip antennas: Typically operate in the range of 300 MHz to 3 GHz, which are often used in applications such as mobile devices, Bluetooth earbuds, smart meters, wireless routers, and RFID systems. Or the low end of super-highfrequency (SHF) chip antennas: Typically operate in the range of 3 GHz to 30 GHz, which are often used in applications such as Industrial Scientific and Medical (ISM) bands, and Ultra-Wide Band (UWB) bands.
The specific frequency range of a chip antenna will depend on factors such as its size, shape, and matching as well as the application for which it is designed.
Why Not Lower Than 433MHz (Frequency Range Overview)
With current design approaches and frequencies below 433MHz, the physical size of the antenna becomes relatively large and thus, cost prohibitive. At the higher costs, these chip antenna solutions below 433MHz lose commercial appeal.
The lower band is also constrained by the wavelength when limiting the package dimensions. For lower frequencies to propagate efficiently, certain elements such as the physical inductance cannot be effectively replaced by an inductor having an equivalent physical length. Although these designs have shown to resonant effectively, the lack of physical elements resulted in unacceptable radiation performance.
Lower frequency antennas require larger sizes than higher frequency antennas because the size of the antenna is directly proportional to the wavelength of the electromagnetic wave it is designed to transmit or receive. The wavelength is inversely proportional to the frequency, according to the formula: wavelength = speed of light / frequency.
This means that at a lower frequency, the wavelength is longer, and a larger antenna is required to efficiently receive or radiate the intended signal. Conversely, at a higher frequency, the wavelength is shorter, and a smaller antenna can be used.
For example, a half-wave dipole antenna (a simple type of antenna) has a length of half the wavelength it is designed to operate at. A dipole antenna designed to operate at a frequency of 1 MHz would have a length of approximately 150 meters, while a dipole antenna designed to operate at a frequency of 1 GHz would have a length of only 15 centimeters. This size difference is significant and can limit the use of lower frequency antennas in certain applications where size constraints are important.
In addition to size considerations, lower frequency antennas may also suffer from lower efficiency due to losses caused by the ground and other obstacles. These losses increase with the size of the antenna and can further limit the range and performance of the antenna. Designers must take these factors into account when selecting an antenna for a particular application.
Why Not Higher Then 10GHz
The capability exists to design and produce chip antennas above 10GHz. These products will be designed/developed and produced when a compelling business case is presented but are not typically offered as off-the-shelf products.
Typical Bandwidth for Chip Antennas & Wide-band VS Multi-band
Energy output and frequency range chip antenna
Bandwidth (Definitions)
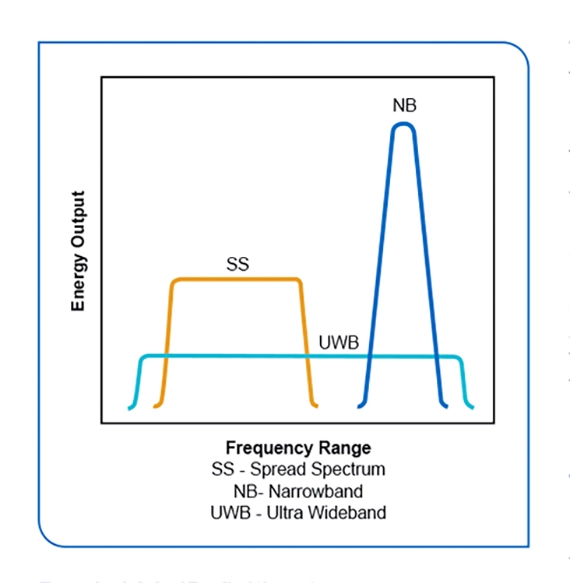
In an antenna, bandwidth refers to the range of frequencies over which the antenna can operate effectively. Specifically, it is the difference between the highest and lowest frequencies within which the antenna can transmit or receive a signal with acceptable radiation patterns, gain, and return-loss performance.
A wide bandwidth is desirable for an antenna as it enables the antenna to operate over a larger range of frequencies, making it more versatile and useful in a variety of applications. A narrow bandwidth, on the other hand, limits the range of frequencies over which the antenna can be used. Bandwidth is also critical in applications where capacitive coupling may shift the antenna resonance.
The bandwidth of an antenna is affected by many factors, including the ground plane, the tuning network, the size and shape of the antenna, the material used to construct it, and the operating frequency.
The bandwidth of a Johanson chip antenna can be measured in terms of percentage bandwidth or absolute bandwidth. Percentage bandwidth is the ratio of the bandwidth to the center frequency of the antenna, expressed as a percentage. Absolute bandwidth is the difference between the upper and lower frequencies within which the antenna can operate effectively, expressed in megahertz (MHz) or gigahertz (GHz).
Typical Bandwidth for Chip Antennas (Bandwidth Definitions)
The typical bandwidth is determined by the application. Many of Johanson's chip antennas are designed for ISM band frequencies, which include BLE and WiFi, are also optimized to operate over a relatively narrow band from 2.4GHz to 2.5GHz, 4% bandwidth. Our UWB antennas operate over much wider bands. For example, Johanson Technology’s unique Ultra-Wide-band antenna, P/N 3100AT51A7200, operates from 3.1GHz to 10.3GHz which is 107% bandwidth.
Wide-band VS Multi-band (Bandwidth Definitions)
Some antennas are multi-band designs while others are wide-band designs.
Multi-band designs work only in the prescribed bands and not between those bands. Wide-band designs function over the entire band of operation
Gain and Isotropic Radiator
Gain (Definitions)
Antenna gain is a measure of the effectiveness of an antenna in radiating or receiving electromagnetic waves in a particular direction. It is the ratio of the radiation intensity of an antenna in a given direction to the radiation intensity that would be produced by an ideal isotropic radiator (a hypothetical point source that radiates uniformly in all directions) radiating the same total power.
In simpler terms, antenna gain describes the degree to which an antenna focuses energy in a particular direction. An antenna with a higher gain will concentrate more energy in a particular direction than one with a lower gain.
Antenna gain is usually expressed in decibels (dB), and the unit of measurement is referred to as dBi (decibels relative to an isotropic radiator). Antenna gain is an important factor in the design and selection of antennas for specific applications.
Antennas with high gain are typically used in long-range communication systems, while low-gain antennas are used for short-range communications or in situations where a more omni-directional radiation pattern is desired.
Isotropic Radiator (Gain Definitions)
An isotropic radiator is a hypothetical point source of electromagnetic waves that radiates uniformly in all directions without any directional preference. In other words, it emits energy with equal intensity in all directions, creating a spherical pattern of radiation.
The concept of an isotropic radiator is used as a reference to compare the performance of other antennas or radiating elements. The gain of an antenna is usually measured with respect to the gain of an isotropic radiator, expressed in decibels (dB), and is referred to as dBi (decibels relative to isotropic).
While an isotropic radiator is an idealized concept and cannot be physically realized, it provides a useful reference for evaluating the performance of real-world antennas and other radiating elements. Since an isotropic radiator radiates energy uniformly in all directions, its radiation pattern is a perfect sphere. However, it is difficult to visualize a perfect sphere in a 2-dimensional image.
Instead, the radiation pattern of an isotropic radiator is often shown as a simple plot of gain versus direction, with the gain being constant in all directions. The plot would be a perfect circle, as shown in the image Figure 1:
isotropic radiator gain definitions chip antennas
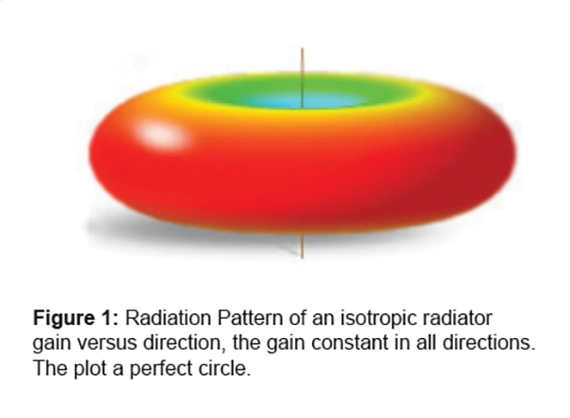
As you can see, the gain (expressed in dBi) is the same in all directions, represented by the circular/ semi-spherical shape of the plot.
The gain in dBi (decibels relative to isotropic) of an isotropic radiator is always 0 dBi. This is because an isotropic radiator is a theoretical point source of electromagnetic radiation that radiates equally in all directions, and there is no direction in which it is "better" than any other direction. Therefore, by definition, its gain relative to itself is 0 dBi.
It's worth noting that while a perfect isotropic radiator doesn't actually exist in the real world, it is a useful reference point for measuring the gain of antennas and other radiating structures. The gain of an antenna is typically measured relative to an isotropic radiator, with positive values indicating that the antenna radiates more power in a particular direction than an isotropic radiator would
Typical Performance & Cause of Variation From Spec
Typical Performance (Gain Definitions)
It is helpful for designers to know the typical chip performance for calculating initial link budget estimates. Chip antennas average gain ranges from -6dBi to +1.0dBi. -2.0dBi could be used for initial estimates.
However, once the final chip antenna selection has been made, the link budget should be recalculated using the average gain of the selected antenna.
Causes of Variation From Spec (Gain Definitions)
Common Causes of Low Gain are:
- Poorly matched chip antenna – specifically the antenna return-loss is lower than the specification.
- The no-ground specified on the data-sheet was not followed in the design.
- The enclosure was made of a material that was conductive or coated with a metal loaded paint, effectively blocking some or all radiation.
- The enclosure was made with a high loss or high absorption material like carbon fiber.
Radiation Patterns
Antenna radiation pattern refers to the directional dependence of the electromagnetic field radiated by an antenna. It describes how the antenna radiates electromagnetic energy into the surrounding space as a function of direction.
The radiation pattern is typically measured in three dimensions, often using a polar coordinate system. In the azimuth plane, the pattern is measured as a function of the angle around the antenna, while in the elevation plane, the pattern is measured as a function of the angle above or below the antenna's axis. The radiation pattern of an antenna can be described mathematically, and it is often displayed as a graph or diagram that shows the intensity of the radiated energy as a function of direction. The pattern can be expressed in terms of gain, directivity, or other parameters that describe the antenna's radiation properties.
Different types of antennas can have different radiation patterns, depending on their design and the frequency of operation. Some antennas, such as directional antennas, radiate more energy in certain directions, while others, such as omni-directional antennas, radiate energy uniformly in all directions. Johanson chip antennas are omni-directional devices.
Typical Performance
Typical Performance (Radiation Patterns Definitions)
Typical radiation pattern performance for Johanson chip antennas is similar to the following:
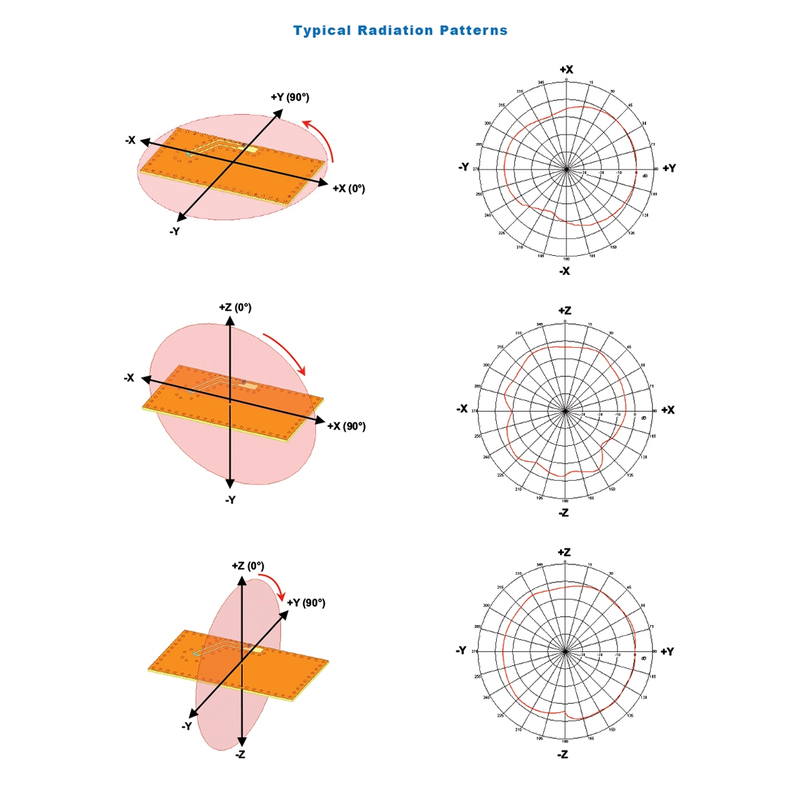
Causes of Variation From Spec
Common causes of poor radiation pattern performance are:
- Large deviation from the geometry of the layout on the data-sheet specification.
- Broken up top RF ground pour (sections of ground vs fluid unobstructed ground).
- No or poor via stitch.
- Very small PCB footprint with respect to the antenna (poor ground)
- Tall conductive components placed immediately adjacent to the no ground area such as batteries, shielding, or metal screws.
- Presence of LCD displays, button, and other conductive objects in the encasement directly above or adjacent to the chip antenna.
Impedance & Matching
Matching refers to the process of optimizing the impedance of an antenna to ensure maximum power transfer between the antenna and the transmitter or receiver. The energy of the RF signal is converted from conducted electromagnetic energy to radiated energy via the antennas as a matched radiating reactive load. Matching is measured in Return Loss in dB.
Johanson chip antennas are typically matched with 1 to 3 capacitors and or inductors. Below is an example of the matching that should be optimized on a fully populated PCB with the enclosure in place.
In this example, the matching components are a 1pF capacitor, 2.7nH inductor and a 3.9nH inductor. The match is optimized by varying the values of those 3 components.
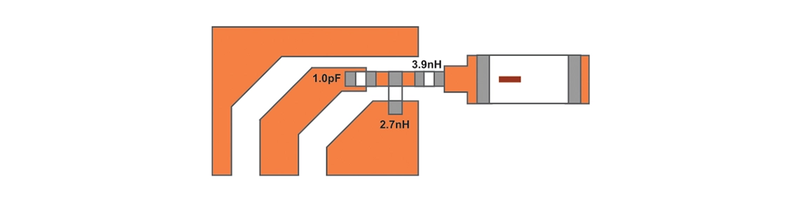
50-Ohm Typical Provided (& Measured) as S-Parameters
Typical return loss for Johanson Chip Antennas is 9.5dB
Other Impedances Like 75-Ohm? Why Not?
It is possible to provide other impedances, but.......not recommended!
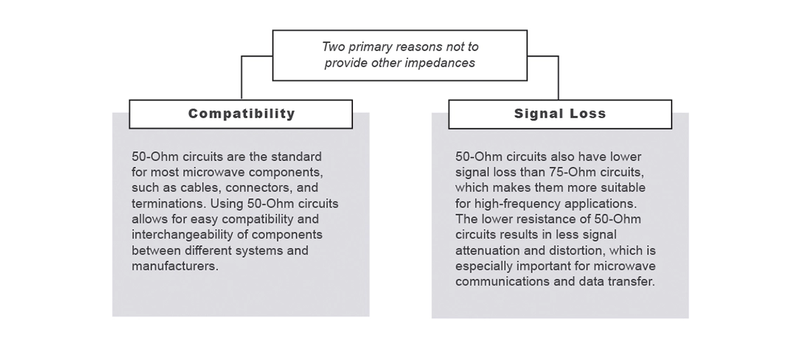
Systems which use 75-Ohm coax are typically much cheaper and commoditized. They also do not have to have a high withstanding voltage. For this reason, 75-Ohm cables are made with less expensive materials and tend to be much cheaper than 50-Ohm cables.
Overall, the use of 50-Ohm circuits is a well-established convention in microwave engineering that offers several advantages in terms of signal transmission, compatibility, power handling, signal loss, and design simplicity.
Chip Antenna Matching Process & Causes of Variation From Spec
Impedance Matching Process (Impedance & Matching Definition)
Typical Steps for Antenna Matching:
- Populate the final PCB with all components
- Cut the antenna feed trace on the PCB to separate it from the filters and transceiver.
- Use a probe or attach a semi-rigid cable to the antenna side of the cur trace.
- Modify the enclosure to allow the semi-rigid cable to exit the enclosure opposite the antenna.
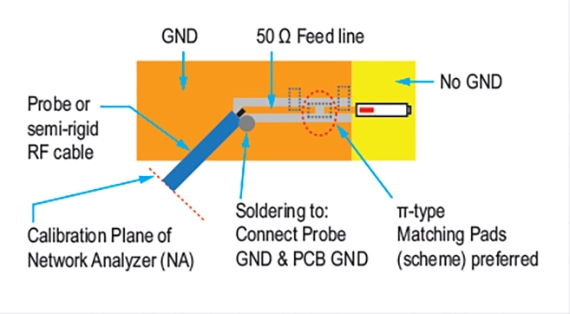
- Using a network analyzer.
- One-port (S11) calibration for N.A. (Network Analyzer) Open-Short-Load for desired operating bandwidth.
- Mount probe (semi-rigid RF cable for our example) onto PCB and connect to N.A.
- Measure S11 of test board without antenna or any matching components and save as: →S11_open →save trace to memory of N.A.
- Measure S11 of test board with antenna and series 0Ω resistor mounted and save as: →S11_antenna.
- Set N.A. to data/memory mode (S11_antenna/ S11_open) and display/save as: →S11_match.
- Match the trace of S11_match to 50Ω (center of Smith chart at the desired frequency) by varying the values of the passive devices.
Causes of Variation From Spec (Impedance & Matching Definition)
Antenna mismatches can occur due to various factors, some of the common causes include:
The dielectric loading aka “capacitive loading" of the enclosure shifts the frequency response requiring a re-tuning.
- Large conductive components placed immediately adjacent the no-ground area.
- Variations in PCB impedance due to fabrication or co-planar waveguide CPWG improper calculation.
- The complete assembly was never matched.
- Unknown inner ground layers intersecting the antenna clearance region (defective PCB).
- Antenna is out of band.
System Effects of a Poor Match and Low Gain
System Effects of Poor Match
A poor match can significantly degrade system performance.
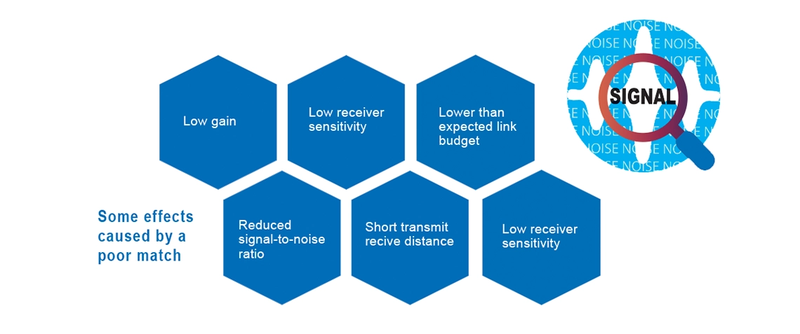
System Effects of Low Gain
Like a poor match, low gain can cause the following system performance issues:
- Reduced signal-to-noise ratio
- Low receiver sensitivity
- Lower than expected link budget
- Short transmit receive distance
- The enclosure is made of, coated with, or contains a non-compatible material
- Enclosure is very lossy at operational frequency.
- A customer made an enclosure out of carbon fiber and the loss of the carbon fiber cause very low gain
- Enclosure is conductive
- A customer used a type of “shiny” paint which contains metal particulates effectively blocking RF signals.
- The enclosure housed a replaceable battery that was located directly over or below the antenna
- The reflection from the battery disrupted the gain and the radiation patterns
Degraded Radiation Patterns and Solder Joint Failure
System Effects of Degraded Radiation (Performance Issues)
Issues with radiation pattern performance can be more subtle and harder to detect. Radiation pattern problems can cause low system performance:
Inconsistent connectivity depending on antenna orientation.
- Possibly no connectivity (represented as nulls in a radiation pattern)
System Effects of Solder Joint Failure – CTE: PCB v. Ceramic (Performance Issues)
The antenna products have an operational temperature range of -40C to +85C. In some cases, the upper range is +125C.
Although the ceramic body and terminations can tolerate extreme temperatures, they cannot tolerate too much thermal shock. If the assemblies are exposed to numerous temperature excursions outside of this range, the solder joint or substrate can become stressed and eventually fail as a fracture due to constant expansion and contractions.
This is caused by the difference in CTE between the Ceramic antenna and the PCB. The coefficient of thermal expansion (CTE) is a measure of how much a material expands or contracts when its temperature changes. The CTE of a material is typically expressed in parts per million per degree Celsius (ppm/°C).
LTCC (Low Temperature Co-Fired Ceramic) and FR4 (Flame Retardant 4) are two commonly used materials for printed circuit boards (PCBs).
The CTE of LTCC ceramic is typically in the range of 3.5-5.5 ppm/°C, depending on the specific composition of the ceramic. The CTE of FR4 PCB material is typically around 13-18 ppm/°C.
Therefore, there is a significant difference in the CTE between LTCC ceramic and FR4 PCB material. This difference can lead to issues such as warping or cracking of the PCB during thermal cycling or temperature changes. It is important to take this difference into account when designing and manufacturing PCBs that use these materials.
Mounting Guidelines, GNSS, Selection Info, & Optimization Process
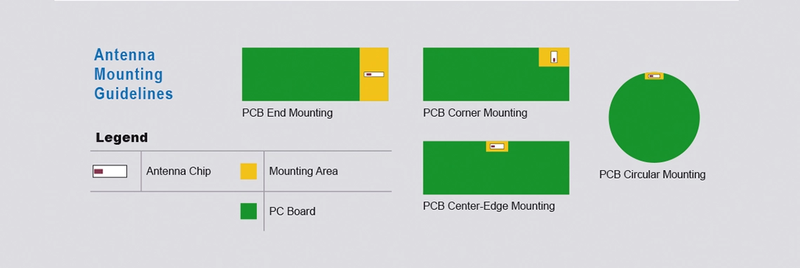
Selection Guide Information:
Note: Refer to the website for latest version of selection guide
Antenna Chip Selection Guide is a useful tool early in the design process when a decision on which Johanson antenna chip/s will be selected.
First, the designer must choose what type of layout is desired based on the product shape and remove allowable antenna chip placement.
The mounting plays a critical role in antenna chip selection.
It is important that the designer understands that the "Antenna Optimization Process" is composed of the following:
All four of these features work together to determine the final system performance. As such, changes to the no-ground area or chip locations relative to the edge of the circuit board can result in substandard performance.
Once the layout type has been selected, then determine the application type and associated operational frequency.
In some cases, the selection guide will provide two antenna chip options. We have identified features that should lead the designer to a specific selection.
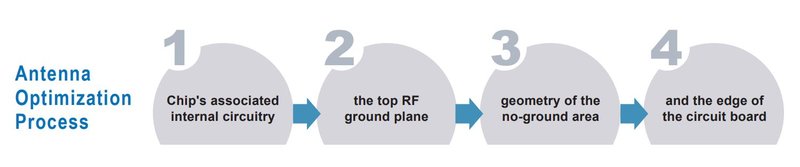
Application Legend & Bluetooth / Wi-Fi / Zigbee Applications
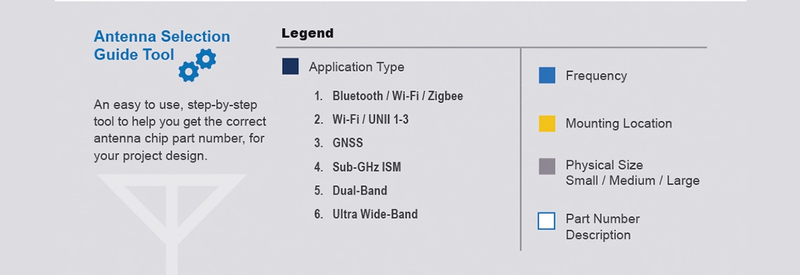
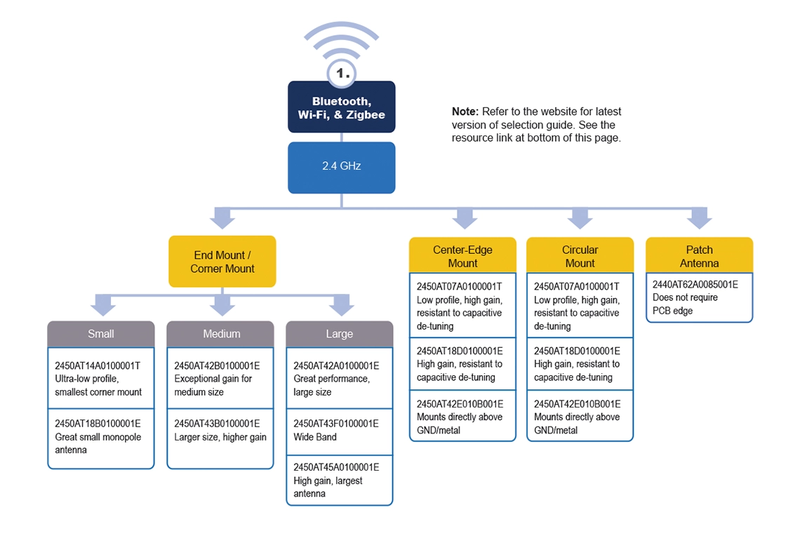
Wi-Fi/UNII 1-3, GNSS, & Sub-GHz ISM
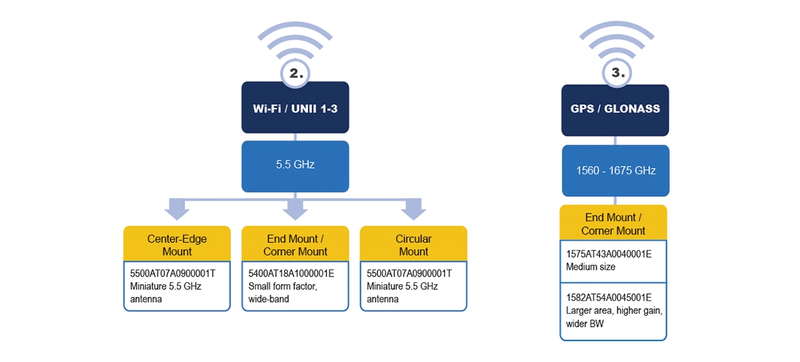
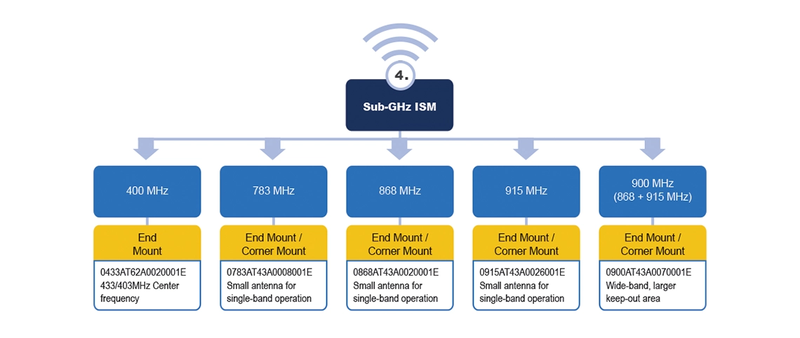
Dual-Band, & GNSS, Ultra Wide-Band Selections Applications
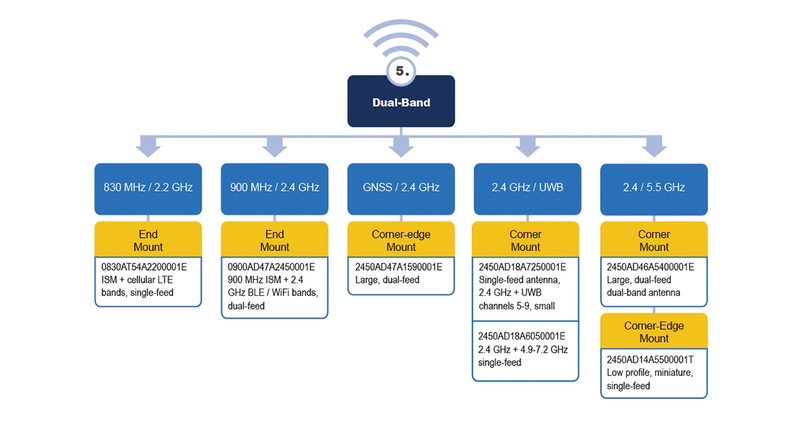
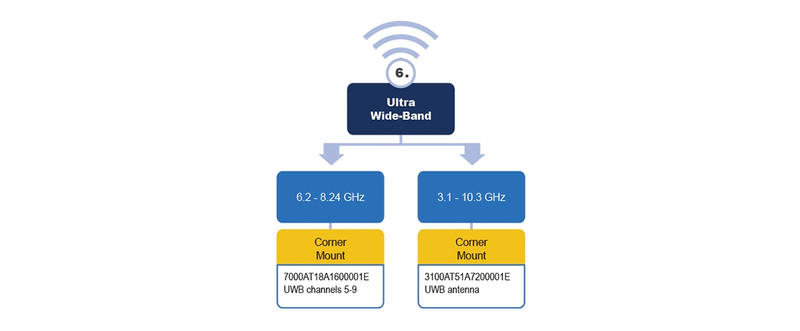
Document, Layout, Tuning Options, & Hardware Review
Document Review (Technical Assistance)
When necessary, an non-disclosure agreement (NDA) can be put in place to facilitate close and detailed technical communication. Johanson takes customer IP very seriously and we are constantly improving our systems to keep all customer details confidential. Most of our design layout reviews are performed in California, USA. Our facility is also equipped to handle secure server communication covered by our ITAR procedures.
Step 1: Layout Review (Technical Assistance)
Johanson offers JTI manufactured ceramic chip antenna customers 2 complimentary RF layout reviews of your PCB by a Johanson Technology (JTI) RF engineer before fabrication to ensure optimum performance. Our engineering team will provide prefab board layout (antenna footprint) suggestions such as, antenna selection, location, and grounding recommendations. Our lab is equipped with calibrated network analyzers and state-of-the-art anechoic test chambers for radiation pattern characterization based on measured data on the client’s PCB.
Option A: Quick Tune Antenna Matching Service (Technical Assistance)
Step 2: Layout Review (Technical Assistance)
Once the layout review and prototype manufacturing has occurred, the only requirement is that clients send Johanson a fully populated PCB: all SMDs including batteries, connectors, and encasements (as they may affect RF resonance) antenna performance mounted and installed. Customers can leave the antenna (optional) and antenna matching components’ slots empty as Johanson will be solder mounting them. The system does not need to be functional. Johanson will feed passive 0dBm signal directly into the antenna-1 for proper isotropic radiation measurements.
This “Quick Tune” service where the antenna on your circuit board (along with all components), is matched for return-loss by calculating the values and part numbers of the inductors and capacitors (Ls & Cs) in the antenna matching network. No gain or radiation patter measurement is taken in this type of service. It will ensure the antenna match is operational at the intended frequencies.
Option B: Thorough Tuning & Performance Varification in Anechoic Chamber (Technical Assistance)
Two complimentary RF layout reviews of your PCB by a Johanson Technology (JTI) engineer before fabrication to ensure optimum radiated performance. Our engineering team will produce prefab board layout (antenna footprint) suggestions, antenna selection, location, and grounding recommendations. We have available state-of-the-art anechoic test chambers for radiation pattern characterization based on measured data on the client’s PCB.
Once the layout review recommendations are implemented and prototype manufacturing has occurred, the only requirement is that clients send us a fully populated PCB: all SMDs including batteries, connectors, and encasements (they affect RF resonance) mounted and installed. The customer can leave the antenna (optional) and antenna matching components’ slots empty as we will be mounting/soldering them ourselves. The balance of the system electronics do not need to be functional; we feed our own passive 0dBm signal directly into the antenna for proper isotropic radiation measurements.
Testing, & Recommendations
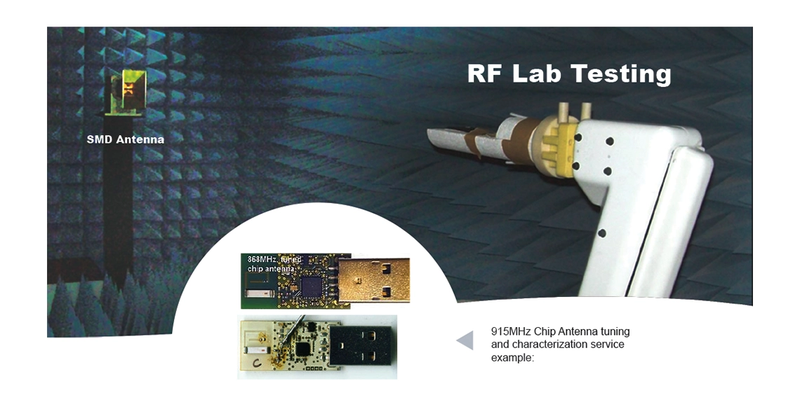
The RF lab will need to prepare the SMD antenna on the assembly shipped to Johanson. The preparation begins by identifying where the antenna is located. If the module is shipped assembled, the lab might ask for disassembly instructions. The next step is to determine the injection point of our calibrated signal. This process is destructive because in most cases the feed trace to the antenna will need to be isolated from the RF source on the PCB. Since the signal is being injected using a probe, additional holes may be drilled in any casings. The goal is to measure the antenna while the module is fully assembled. Once the probe is in place, our technicians use a Smith chart and one of Johanson’s tuning kits (e.g., EIA 0402 kit S402DS, L402DC, L402W, S402TS, L/C_402DS) to get the impedance at 50-Ohms. Note: most Johanson chip antennas do not naturally have a 50 Ohm impedance.
The specific, order-able part numbers of these matching Inductors and capacitors (L & Cs) are provided in the report.
Once the antenna is confirmed to be tuned to the data-sheet specification, the next step is to measure the radiated performance in an anechoic chamber. This measurement takes data which provides 2D cuts at specified reference planes and a 3D plot representing the Johanson chip antenna on the customer module
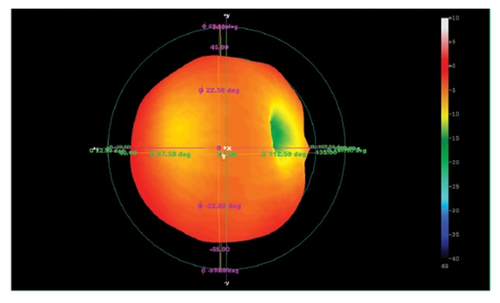
Client is then sent copies of the new matching circuit schematic with their corresponding values and part numbers, measured radiated data, and patterns with their corresponding radiated efficiency and gain figures on your PCB. Sometimes this process may require Johanson Technology to modify your board in their lab, and to add probes through your enclosure/ housing.
Assemblies may be returned to customers at their request.
Testing, & Recommendations
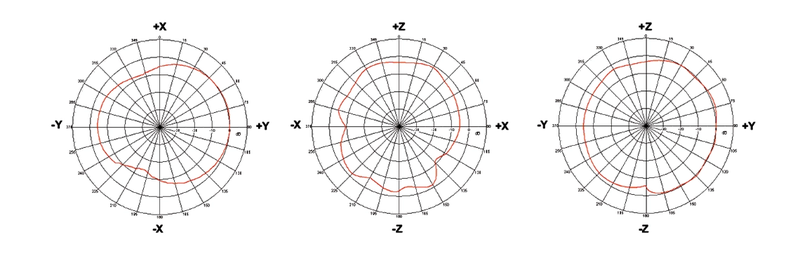
Please confirm with an engineer prior to sending your module. Sending modules without a confirmation risks them getting misplaced.
The ultimate goal is to optimize “Over-The-Air” performance of your design using Johanson’s extensive design knowledge and application optimization expertise for market success, this entire process takes 2 to 3 weeks, depending on the complexity of the design and environment.
Shipping address for prototypes to be tuned & characterized is:
Johanson Technology, Inc
Attention: Name of the project engineer
4001 Calle Tecate
Camarillo, CA 93012
USA
Custom Chip Antennas
Johanson welcomes any inquiry related to LTCC antenna specifications which may not be in the catalog and will consider your needs for a unique/ custom antenna solution.
The design and tooling costs for a new antenna can be substantial. Thus, it is important that we also understand your anticipated demand for this new product. Although not an absolute requirement, an approximate minimum annual quantity of 1,000,000 pieces and a minimum of 3 years of production should be used to estimate the feasibility of developing a new chip antenna. Don't miss the opportunity to work with our outstanding design engineers.
Visit our website for more information. We look forward to assisting you with your unique design requirements See "RESOURCE" below
The Johanson Technical team will review your specification or requirements document.
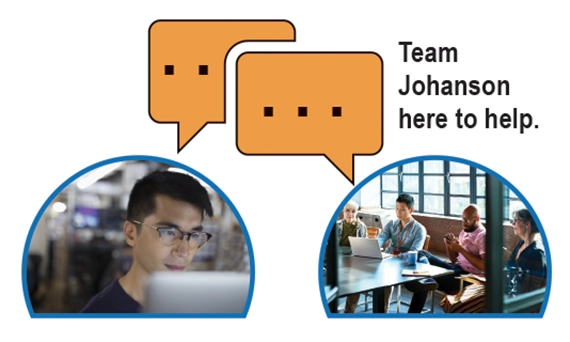
Antennas Terminology
Bandwidth:
The range of frequencies over which an antenna can operate with good performance.
Beam-width:
The angular width of the main lobe of an antenna radiation pattern.
Directivity:
A measure of how well an antenna concentrates energy in a particular direction, expressed as a ratio of the power radiated in a specific direction to the total power radiated.
Gain:
The measure of the ability of an antenna to direct energy in a particular direction compared to an isotropic radiator.
Impedance:
The opposition of an antenna to the flow of alternating current (AC), measured in ohms.
Isotropic Radiator:
An idealized antenna that radiates energy equally in all directions.
Polarization:
The orientation of the electric field of the radiated wave with respect to the ground plane.
Radiation Pattern:
The directional distribution of radiated energy from an antenna in three-dimensional space.
Return Loss:
A measure of the amount of power reflected back towards the source when a signal is transmitted through a transmission line or antenna. It is usually expressed in decibels (dB) and is a measure of the impedance mismatch between the source and the load.
Resonance:
The condition when an antenna is perfectly matched to the frequency of the applied signal.
VSWR (Voltage Standing Wave Ratio):
The ratio of the maximum voltage to minimum voltage along the transmission line connected to the antenna.
Types of Antenna Chips
Planar Inverted-F Antenna (PIFA):
An antenna chip that has a rectangular or square radiating element connected to the feedline by a shorting pin. Widely used in mobile phones and other portable devices due to its compact size and low profile.
Meander Line Antenna:
An antenna chip that uses a zigzag or meandering line as the radiating element. Often used in applications that require a narrow bandwidth.
Monopole Antenna:
An antenna chip that is constructed using a simple, single-element structure. Often used in applications that require a broad bandwidth and high gain.
Dipole or Folded Dipole Antenna:
An antenna chip that consists of two identical conductive elements that are parallel to each other and oriented in the same direction.
Slot Antenna:
An antenna chip that uses a slot in the ground plane as the radiating element. Often used in applications that require a high radiation efficiency and low profile.
Ceramic Patch Antenna:
An antenna chip that uses a ceramic material as the substrate. Often used in applications that require a high radiation efficiency and low loss.
Inverted-L Antenna:
An antenna chip that has a vertical wire that is connected to a horizontal wire, creating an "L" shape.